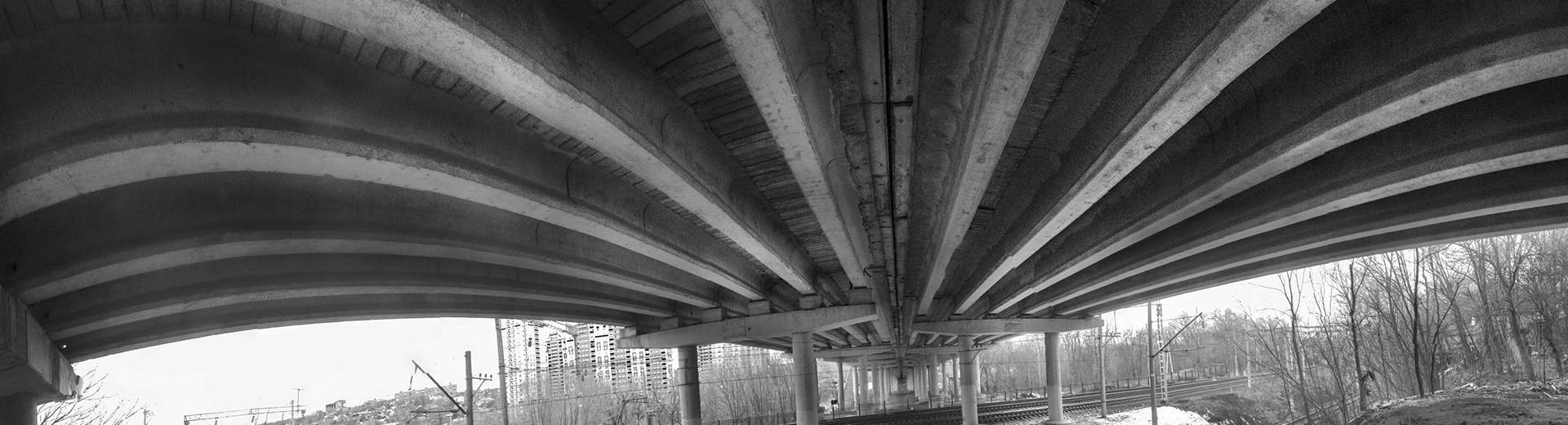
Fiber optic sensor technology for measuring constraints
The use of the fiber optic sensor technology for measuring constraints is particularly well suited. Compared to conventional strain gauge technology (resistant wire gauges, electrical deformation gauges, etc) that requires mostly a “Wheatstone bridge” type construction, fiber optic sensors such as ” Bragg Gratings ” can be implemented directly and easily on the elements under constraint. The Fiber Bragg Gratings corresponding to a very small part (1 to a few millimeters) of an extra sensitive optical fiber, it is possible to install a multitude of sensors or “strain gauges” on one single optical fiber. In addition, an interrogator unit is capable to monitor more than 120 points of measures (or many more through the use of an optical multiplexing system) spread over one or more optical fibers.
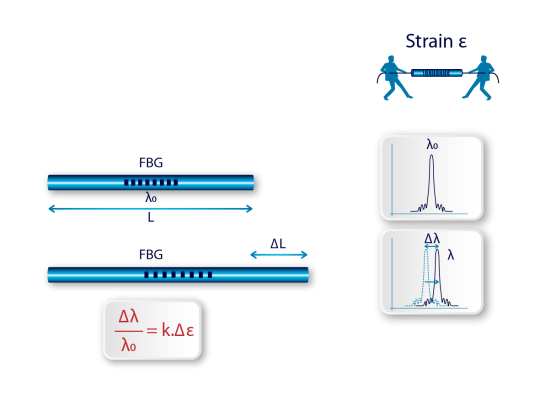
Perfectly optimized and fully adaptive
This stress measurement by Fiber Bragg Grating technology has many advantages:
- High Performance Measurements
- Total immunity to electromagnetic interferences
- Great robustness and reliability in environments subject to high vibration and shock
- Very low losses and transport of measurements on very large distances (hundreds of meters to several kilometers)
- Compliance with explosions-proof standards and ATEX directives
- Compact and very low intrusiveness
- Distributed measurements and network set up of a large number of individually addressable sensors
Perfectly optimized and fully adaptive, the wide range of Fiber Bragg Grating measuring units developed by LGS by Texys enables a set up adapted to different uses to ensure the optimization of cost and performance.
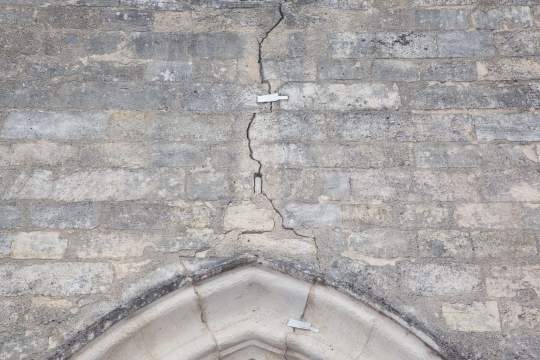
Wind mill monitoring
In order to detect the intrinsic failures of a wind turbine blade and thus ensure the operator that the machine is stopped and restarted in case of an icing problem, or simply to improve the control system of the wind turbine to optimize its production, the wind turbine blades can be equipped with a continuous monitoring system.
To monitor the stresses seen by metal masts, to control the tightening of fasteners, or to follow the evolution of cracks related to the aging of concrete masts, the masts can be equipped with a continuous monitoring system.
To monitor temperatures in the generator windings, to track temperature increases in the hydraulic circuits of the gearboxes or to monitor hot spots in the electrical circuits, a continuous monitoring system can be used.
All of these continuous monitoring system needs can be covered by the use of independent fiber optic sensors or linked to a common central unit. The various fiber optic sensor technologies offered by LGS by Texys are perfectly adapted to the specific environmental constraints of onshore and offshore wind turbines.
Types of applications with Fiber Optic for Wind Turbine Monitoring
- Ice detection on blades
- Balance control of blades
- Detecting defects on blades
- Measure of effort on blades
- Detection of lightning strikes on blades
- Control/Detection of cracks in concrete masts
- Control of mast mounting elements
- Monitoring of constraints on metal masts
- Detection of hot points (generator winding, disconnectors…)
- Measurement of oil temperatures in hydraulic circuits
- Monitoring of constraints on bearings
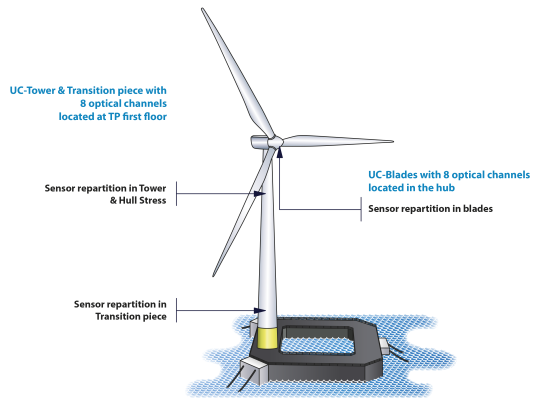